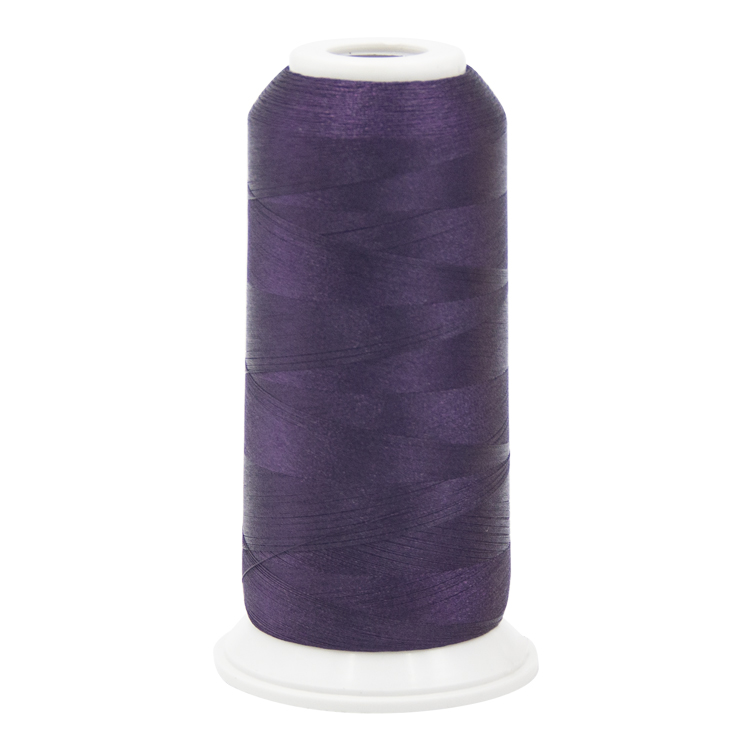
Cause of ring spinning defects and process control
The maturity, fiber length, linear density and strength of raw cotton are the basic factors that determine the yarn quality, which are closely related to the maturity of raw cotton. Because the maturity of seed cotton is poor and the strength of single fiber is small, it is easy to transfer longitudinally along the length direction of the sliver in the drafting process and tend to concentrate, winding and twisting to form fiber defects such as neps and wires. In addition, the quality of ginning of seed cotton is very important to the quality of yarn and the formation of yarn defects. The grading conditions and reference indexes of ginning quality are determined by the number of defects and impurities in raw cotton, and the main defects include yarn, soft seed skin, rigid piece, broken seed, sterile seed, with fiber seed chips and neps. Because of the small defects of the fiber seeds and neps, which are easy to be tangled with the fiber and not easy to be removed, it is very harmful to the quality of the subsequent yarn. However, excessive cleaning of lint will lead to the increase of small seed chips and short fibers in raw cotton, which will also affect the final yarn quality. In addition, the amount of cotton recycled by enterprises will also lead to yarn defects, which should be used carefully and reasonably.
Process control of each process
1 carding
The carding process is to separate the bundle and block fibers into a single fiber state so as to comb the fibers carefully. Good fiber separation and straightness parallelism are important prerequisites for improving yarn evenness and reducing yarn defects. Generally, the fiber separation and straightening are reflected by the clarity of cotton web, and the fiber separation is mainly realized by reasonable and accurate on-line technology. On the basis of "four fronts and one standard" (Xilin, rotary cover plate, doffer and roller clothing are sharp, and the spacing between clothing is accurate), the reasonable selection of clothing configuration plays a key role in the growth of short fiber.
2 rolls, combing preparation
The winding process mainly solves the problem of fiber sticking. The sticking problem will not only make the fiber strip produce coarseness and details, but also produce hook fiber and disordered fiber, which will increase yarn defects and noil. The solution to the sticking is to control the temperature and humidity, adjust the pressure of the small coil, and reduce the drawing times of pre merging and strip coil. Because the comber can straighten the front hook of the fiber, it should be ensured that the front hook of the fiber accounts for the majority of the small coils fed into the comber in the combing preparation process, so as to play the role of the comber in straightening and parallel combing the fiber.
3 combing
The theoretical fiber straightness of the comber is about 94%. When the working state of the comber is bad or the fiber varieties are different, the new hook fiber will be produced due to the burr, hole and bad joint of the comber. The main solution is to control the temperature and humidity of the workshop scientifically. The temperature control is about 28 ℃, the relative humidity control is 55% - 58%, the surface roughness of the channel is good, and the technology is good The upper carriage shall be accurate, the installation size of top comb shall be reasonable, and the installation of each collector shall be accurate. Especially for long staple cotton, the fiber is long, the head is poor, the cotton layer is easy to spread to both sides, and the hook fiber is produced by hitting the collector.
4 pre drawing
Fiber straightening is mainly realized by combing and drawing. The hook fibers formed in carding machine are mainly the back hook, accounting for about 50% of the hook fibers, the front hook for 30%, and the other 20% are irregular hook fibers. The hook fiber will not only form yarn defects, but also form neps. The pre drawing process is mainly to straighten the front hook, and the draft ratio of the rear area should be controlled at about 1.7, which is conducive to eliminating the front hook.
5 drawing
In addition to setting reasonable process and accurate upper carriage in combing and drawing process, it is also important to adjust the uniform strength of nodes; when rough and detail are detected by concave convex roller, the speed change advance or lag of middle and rear roller will directly affect the product quality. In addition, the cot around the flower, suction is not normal, will also affect the number of yarn defects. In general, a smaller draft multiple and a larger roller spacing should be used to make the front area draft intensively, which can prevent additional unevenness caused by draft and help to reduce coarseness and details. At present, new spinning machines such as comber and drawing frame have automatic pressure relief devices, and the setting of pressure relief time is very important, because there is a certain tension between fibers during pressure relief, which will produce relative slip and lead to details.
6 roving
The main causes of yarn defects in roving process are abnormal rotation and clutching of upper and lower cashmere sleeves, improper use of cotton collectors, warping of cots, aging and cracking of upper and lower cots, and unevenness of roving strips. The solution is to ensure good surface roughness of each yarn passage, normal pressure of drafting system, and prevent cots, rollers from slipping, cots from concave, and correct gear engagement , and control the reasonable cycle of rubber ring replacement.
7 spinning
As the last process of spinning, ring spinning frame has a decisive influence on yarn quality. In general, the back spacing should be larger and the draft multiple should be smaller. When the cots are wound with fibers, not only the cots that are wound with fibers should be cleaned, but the adjacent cots should also be treated; when the fibers are wound seriously, the cots must be replaced. The control of relative humidity in spinning workshop should be slightly lower than that in roving workshop, so that the fiber is in a state of micro dehumidification; if the relative humidity is too high, the friction between the fiber and the steel wire ring and the steel ring will increase, the number of broken ends and flying flowers will increase, resulting in the curling of cots and rubber rings. Reducing the dust content in the workshop can reduce the accumulation of flying flowers on the roving surface and reduce the probability of flying flowers attaching between the yarn unwinding and the bell mouth. Clean the passage, reduce the rubber roller, rubber ring and roller winding flowers, and timely remove the foreign matters on the roller surface to ensure the smooth surface of roller; at the same time, all the flying flowers in the lower rubber ring need to be cleaned to reduce the flying flowers in the drafting area. Strictly implement the operation rules, especially the spinning draft part to reduce the flying flowers attached to the cradle. To ensure the quality of semi-finished products, it is strictly prohibited to move and place the sliver and roving randomly. When pulling the sliver, the sliver should be pulled gently to prevent the sliver from getting fluffed; after the roving is dropped, the surface of the roving should be avoided to touch the wool. Improve the operation skills, especially the spinning joint, reduce the defects.
No matter what type of drafting mechanism is in modern ring spinning, there is a floating area length. Because the short fiber is difficult to control when passing through the drafting area, the fiber speed change point is unstable, resulting in coarseness and details, resulting in yarn defects increasing with the increase of drafting times.
8 winding
In the winding process, it is necessary to improve the quality of the air splicing joint of the winder, select the best splicing process parameters, eliminate spindle difference, timely repair the spindle with poor joint, carry out joint spot check, and timely feedback the abnormal spindle.
Flying flower
The flying flower is mainly composed of short fibers. The influence of the short fibers whose length is less than 10 mm on the yarn evenness and yarn defects is greater than that of the fibers whose length is 10 MM-16 mm. Therefore, in cotton blending, not only the short fibers whose length is less than 16 mm, but also the short fibers whose length is less than 10 mm should be controlled, because the floating length of the main draft area of the ring spinning frame is about 10 mm. When the air flow around the machine is large or to a certain extent, the flying flowers will randomly fall into the semi-finished products being spun to form yarn defects. In addition, the surface of semi-finished products with long storage time will be hairy, and the direction of hairy fiber entering the yarn strip is random, and yarn defects will be formed when it contacts and rubs with the machine parts again; therefore, during the production process, attention should be paid to the control of dust content in the workshop, and the machine should be cleaned and maintained regularly and timely according to different requirements; the semi-finished products should pay attention to the prevention of dust and short hair, and timely make Use to avoid long storage time.
There are many factors that lead to yarn defects, involving a wide range. Textile mills should improve the quality of raw cotton, the rationality of spinning technology and the standardized operation and management of each process in the workshop, so as to reduce yarn defects and improve the yarn quality.