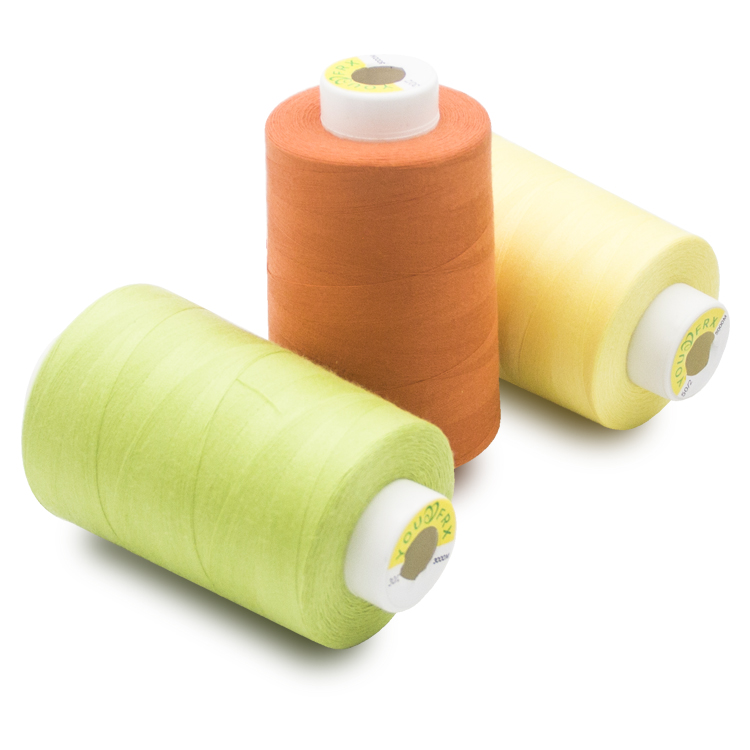
The cause analysis and control of the cross bar of knitted yarn(1/4)
1 Preface
Knitted fabric has the characteristics of soft texture, moisture absorption, air permeability, elasticity and drape. Knitted clothing is comfortable, close fitting, unrestrained, free and fashionable, which can fully reflect the curve of human body. The Pearl River Delta is adjacent to Hong Kong and Macao, and knitted fabrics are more colorful. It has entered the development stage of multi-functional, fashionable and high-grade. New knitted fabrics with various texture effects and different functions have been developed, bringing unprecedented sensory and visual effects to knitwear. At present, knitted fabric is widely used in clothing fabric, medium and high-grade underwear, lining, home textile and other products, and is deeply loved by the majority of consumers.
Knitted grey fabric is made of knitting needles to turn each yarn into a loop separately, and then the loops are knitted in series with each other. The structure of knitted fabric is loose, there are many gaps in the loop and between the loop and the loop, and the hook and string structure of the loop has the characteristics of separation. Therefore, the requirements of knitting yarn are relatively high. The quality of knitting yarn directly affects the quality of knitted fabric surface, weaving characteristics and Compared with the woven yarn, the knitting yarn emphasizes the quality characteristics of yarn, such as evenness, slug, nep, strength, hairiness, twist and so on. The rung of knitted fabric is an important index that affects the quality of knitted fabric, and the reasons for the rung are raw materials, yarn quality stability, weaving, dyeing and finishing processes, etc. This paper discusses the reasons for the production of knitted fabric rung in the process of spinning production and how to meet the requirements of knitted fabric.
2. Analysis of the causes of knitting fabric rungs during spinning
2.1 inherent color difference of raw materials: different cotton varieties, grades, regions, soils, climates, fertilization, harvest time, etc., will produce different color differences in its appearance. Chemical fiber raw materials, such as viscose fiber, also produce the color difference phenomenon of yellow and white fiber in the process of raw material production and processing, which mainly displays in the difference of whiteness, the change of residual sulfur content, the difference of raw material batch in the production process, etc.
2.2 too large difference of maturity of raw cotton in cotton blending results in color difference in dyeing: cotton fiber with good maturity is easy to absorb color, while cotton fiber with poor maturity is not easy to absorb color. If the maturity difference of raw cotton is too large in cotton blending, it will lead to different fiber dyeing ability and color difference.
2.3 uneven blending in the cotton cleaning process.
2.4 unreasonable cotton blending process and batch receiving.
2.5 yellow and white yarn caused by the difference of strong twist or weak twist caused by the difference of spinning speed
2.6 the yarn line is long and thick, the long details are obviously accumulated, the yarn hairiness is different greatly, and the yarn weight is uneven seriously.